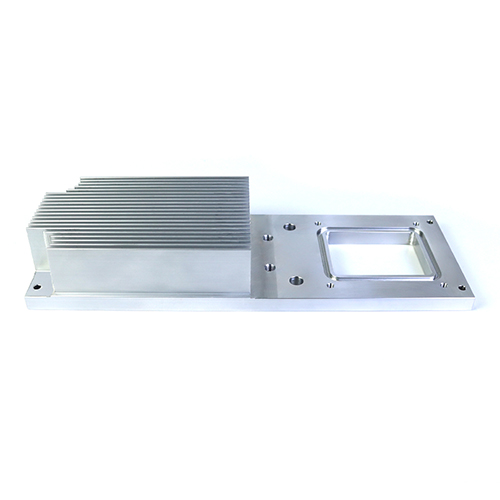
Technological Advancements
In the wave of modern manufacturing development, the field of aluminum alloy CNC milling parts is undergoing remarkable technological innovations, and a series of new breakthroughs have brought unprecedented opportunities for related industries.
In terms of machining accuracy, advanced error compensation technology has become a key highlight. By integrating high-precision sensors and intelligent algorithms into the CNC system, it is possible to monitor and compensate for errors caused by factors such as thermal deformation and tool wear during the milling process in real time. Nowadays, the dimensional accuracy of aluminum alloy CNC milling parts can be stably controlled at the micrometer level, which is of great significance in the aerospace field. For example, for certain aluminum alloy key components of aircraft engines, higher precision means better performance and reliability, which can effectively reduce safety hazards during flight.
There have also been new developments in high-speed cutting technology. New types of tool materials and coating technologies have emerged, which have higher hardness, wear resistance, and heat resistance. When CNC milling aluminum alloy parts, the cutting speed is significantly increased compared to traditional processes, while ensuring good machining surface quality. This not only greatly shortens processing time and improves production efficiency, but also enables faster production of high-precision aluminum alloy wheels, engine cylinders, and other components for automobiles in the automotive manufacturing industry, accelerating the production cycle and reducing costs.
In addition, multi axis linkage machining technology is becoming increasingly mature. Five axis, six axis, and even more axis CNC milling equipment are constantly being optimized. Through multi axis linkage, it is possible to achieve one-time complete processing of complex shaped aluminum alloy parts, avoiding errors caused by multiple clamping. In the field of medical devices, for complex shaped aluminum alloy orthopedic implants or precision surgical instruments, this technological advancement can ensure that the geometric shape and surface quality of the parts fully meet the high standards of medical use, providing more reliable guarantees for the treatment effect of patients.
Intelligent programming and simulation technology is also a major breakthrough. With the help of advanced computer-aided manufacturing (CAM) software, programmers can generate optimized milling programs more quickly and accurately. In the simulation stage before processing, the entire milling process can be accurately simulated to detect possible collision, overcutting and other issues in advance, and adjust the processing strategy in a timely manner. This effectively reduces the cost of trial and error and improves the success rate of production for parts with extremely high precision requirements such as aluminum alloy heat sinks and precision structural components in the field of electronic communication.
The significant technological advancements in CNC milling of aluminum alloy parts are like powerful engines, driving many industries such as aerospace, automotive, medical, and electronic communication towards higher quality and efficiency, and injecting continuous power into the upgrading of global manufacturing.
Excellent advantages
The advantages of aluminum alloy CNC milling parts in news reports: its high-precision and high-quality processing characteristics meet the needs of high-end industries such as aerospace and automotive, and help promote the lightweight and high-performance development of the industry. It is an excellent material to showcase the cutting-edge technological achievements of modern manufacturing.
Demand And Job Stability
In the current booming manufacturing industry, aluminum alloy CNC milling parts have attracted much attention, and their news value is reflected in the rapid growth of demand and excellent performance in work stability.
From a demand perspective, the aerospace industry has an urgent need for it. The development of new fighter jets and spacecraft requires aluminum alloy CNC milling parts to meet the characteristics of high strength, low weight, and extreme environmental resistance to ensure flight safety and performance. For example, the key connecting components of airplane wings must be precisely machined without any deviation. The lightweight revolution in the automotive industry has also led to a large demand for aluminum alloy milling parts. The use of such parts in engine cylinder blocks, chassis and other components can effectively reduce vehicle weight and improve fuel economy. In the field of medical devices, the manufacturing of orthopedic implants and high-end surgical instruments requires extremely high precision and biocompatibility of parts, making aluminum alloy CNC milling parts an ideal choice. In the electronic communication industry, 5G base station equipment and smartphones have strict requirements for heat dissipation performance. The heat dissipation advantage of aluminum alloy milling parts is highlighted, and its machining accuracy determines the stable operation of the equipment.
In terms of work stability, aluminum alloy CNC milling parts perform excellently. The maturity of CNC milling technology enables machining accuracy to reach micrometer level, ensuring high consistency of part dimensions. Under complex working conditions, the parts can operate stably. Taking aluminum alloy parts in aviation engines as an example, they can work stably for a long time in harsh environments such as high temperature, high pressure, and high-speed rotation due to their precise processing and excellent materials, avoiding safety accidents caused by part failures. During the driving process of a car, aluminum alloy milling parts can maintain stability and ensure the vehicle's handling performance even under complex mechanical loads. In medical equipment, these components can maintain stable performance and ensure medical effectiveness in frequent use and complex human environments. This kind of job stability comes from advanced processing technology and strict quality inspection system, from raw material screening to processing process monitoring, and then to finished product testing, each step builds a solid foundation for the stability of the parts.
Summary
In today's advanced manufacturing field, aluminum alloy CNC milling parts have become the focus of the industry due to their outstanding performance. Through CNC milling technology, the machining accuracy of aluminum alloy parts can reach the micrometer level, and both complex geometric shapes and fine internal structures can be accurately presented. This processing method not only significantly improves production efficiency and shortens manufacturing cycles, but also effectively reduces manual errors, ensuring high stability of product quality. In many key industries such as aerospace, automotive manufacturing, and electronic communication, aluminum alloy CNC milling parts have demonstrated irreplaceable advantages, providing strong support for the performance improvement and lightweight design of high-end equipment. Its environmentally friendly and energy-saving processing process also conforms to the trend of the times, undoubtedly an important driving force for the high-quality development of modern manufacturing industry, leading the field of parts processing to move towards greater precision, efficiency, and greenness.
Post time: Nov-08-2024