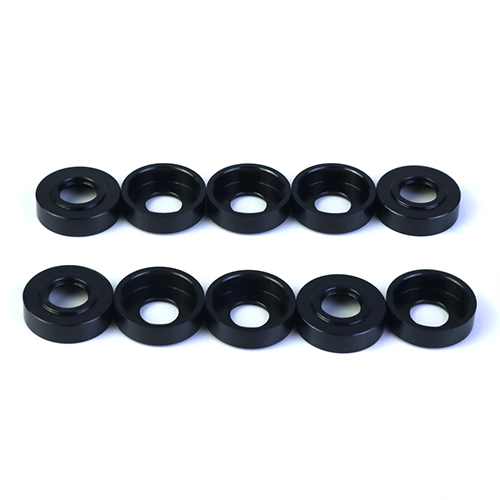
In today’s fast-paced industrial landscape, the demand for customized CNC machining parts is soaring. Whether you're in the automotive, aerospace, medical, or electronics sector, businesses are increasingly turning to CNC (Computer Numerical Control) machining for high-precision, tailored solutions that meet their unique specifications. With industries pushing the boundaries of innovation, customized CNC parts are fast becoming a game-changer, offering unparalleled accuracy, flexibility, and cost-efficiency in production.
Key Benefits of Customized CNC Machining Parts
Precision and Accuracy: CNC machines are capable of achieving tolerances as tight as a few microns, ensuring that parts are crafted with an exceptional level of detail and consistency. This level of accuracy is critical for industries such as aerospace and medical devices, where even the smallest deviation from specifications can result in catastrophic failures.
Flexibility in Design: One of the major advantages of CNC machining is its ability to produce complex geometries that traditional manufacturing methods can’t achieve. Designers and engineers can create intricate designs, incorporating features like internal cavities, unique textures, and multi-axis contours, without compromising on quality or functionality.
Cost-Effectiveness: While CNC machining is often associated with high-end production, it can also be surprisingly cost-effective, especially when producing small runs or customized parts. For businesses, this translates into reduced production costs and the ability to make on-demand parts without the overhead of traditional mass manufacturing methods.
Quick Turnaround Times: With the use of advanced CNC machines, businesses can go from design to production in a fraction of the time it would take using traditional methods. This is crucial in industries like automotive and electronics, where rapid prototyping and quick time-to-market are essential for staying competitive.
Material Variety: Customized CNC machining supports a wide range of materials—metals, plastics, composites, and more. Whether you're crafting aluminum, stainless steel, titanium, or even exotic alloys, CNC machining can work with diverse materials to meet the specific requirements of each project.
Industries Driving Demand for Customized CNC Parts
Aerospace: Precision and reliability are paramount in aerospace, where parts like turbine blades, engine components, and structural elements must meet stringent standards. CNC machining offers the level of accuracy needed to ensure the safety and performance of critical aerospace systems.
Automotive: The automotive industry relies on CNC machining for parts such as engine blocks, gear shafts, and suspension components. With the rise of electric vehicles (EVs) and autonomous driving technology, customized CNC parts are becoming essential for producing lightweight, high-performance components that enhance vehicle efficiency and safety.
Medical Devices: In the medical field, customized CNC parts are crucial for creating complex surgical instruments, implants, and diagnostic equipment. The precision required in these parts is non-negotiable, as even the smallest defect can compromise patient safety.
Electronics: The ever-evolving electronics industry relies on CNC machining to create highly customized parts like casings, connectors, and microcomponents. With devices getting smaller and more sophisticated, the demand for precision-made, tailor-fitted parts continues to grow.
Renewable Energy: As the world shifts toward sustainable energy solutions, CNC machining is playing a key role in producing parts for wind turbines, solar panels, and energy storage systems. These parts must withstand extreme conditions, and custom CNC machining ensures their durability and functionality
The Technology Behind Customized CNC Machining Parts
The CNC machining process involves using computer-controlled machines to precisely cut, drill, mill, or shape material into a specific design. With advanced software like CAD (Computer-Aided Design) and CAM (Computer-Aided Manufacturing), manufacturers can create highly detailed 3D models of the parts before production, ensuring that every design element is accounted for.
· Milling: Cutting and shaping materials by rotating a cutting tool against the workpiece.
· Turning: Rotating the material while a stationary cutting tool shapes it.
· Drilling: Creating holes with precision.
· Grinding: Achieving ultra-smooth finishes and high precision.
The Road Ahead for Customized CNC Machining
Looking to the future, the demand for customized CNC machining parts is expected to continue growing. With industries focusing on high-quality, low-volume, and highly specialized products, CNC machining offers a cost-effective solution for businesses to meet these demands. Moreover, as automation and AI-driven technologies become more prevalent in manufacturing, the ability to quickly adapt to changes in design and production schedules will only enhance the value of customized CNC machining.
For businesses striving to stay ahead of the curve, investing in customized CNC machining is not just a smart move—it's a necessity. As technology advances and customization becomes even more critical to staying competitive, the market for precision-engineered, custom CNC parts will only continue to expand, shaping the future of manufacturing for years to come.
Conclusion
Whether you're designing the next big innovation in automotive tech, crafting life-saving medical devices, or building cutting-edge aerospace components, customized CNC machining parts are essential to bringing your vision to life. Offering precision, flexibility, and cost-effectiveness, CNC machining is revolutionizing industries and making tailored manufacturing solutions more accessible than ever. As the demand for high-quality, customized parts continues to grow, the future of manufacturing is increasingly being defined by CNC technology.
Post time: Nov-14-2024