In the relentless pursuit of productivity and efficiency, the manufacturing industry is witnessing a surge in discussions surrounding high-speed machining techniques and cutting-edge tooling innovations. With a focus on maximizing output while minimizing cycle times, manufacturers are exploring advanced tool materials, coatings, and geometries, alongside strategies for optimizing cutting parameters and reducing tool wear.
High-speed machining has long been touted as a game-changer in the manufacturing realm, enabling faster production cycles and improved precision. However, as demands for higher efficiency and tighter tolerances escalate, the quest for innovative machining solutions has intensified. This has led to a renewed interest in exploring the frontiers of tooling technology.
One of the primary drivers behind this trend is the development of advanced tool materials, which offer enhanced durability, heat resistance, and cutting performance. Materials such as ceramic, carbide, and cubic boron nitride (CBN) are gaining traction for their ability to withstand the rigors of high-speed machining, resulting in longer tool life and reduced downtime.
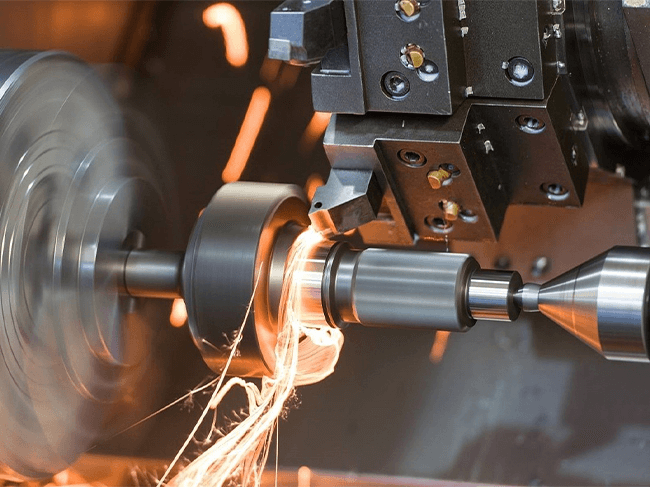
Moreover, advancements in tool coatings have revolutionized the machining landscape, offering improved lubricity, wear resistance, and thermal stability. Nano-coatings, diamond-like carbon (DLC) coatings, and titanium nitride (TiN) coatings are among the innovative solutions that are enabling higher cutting speeds and feeds while minimizing friction and chip adhesion.
In addition to materials and coatings, tool geometries play a crucial role in optimizing machining performance. Complex geometries, such as variable helix angles, chip breakers, and wiper edges, are designed to improve chip evacuation, reduce cutting forces, and enhance surface finish. By leveraging these geometrical innovations, manufacturers can achieve higher material removal rates and superior part quality.
Furthermore, the optimization of cutting parameters is essential for maximizing the efficiency of high-speed machining operations. Parameters such as spindle speed, feed rate, and depth of cut must be carefully calibrated to balance cutting forces, tool life, and surface finish. Through advanced machining simulations and real-time monitoring systems, manufacturers can fine-tune these parameters to achieve optimal performance while minimizing tool wear and material waste.
Despite the remarkable progress in high-speed machining and tooling innovations, challenges persist, including the need for skilled workforce training, investment in state-of-the-art equipment, and integration of digital technologies for process optimization. However, the potential rewards are substantial, including increased productivity, reduced lead times, and enhanced competitiveness in the global marketplace.
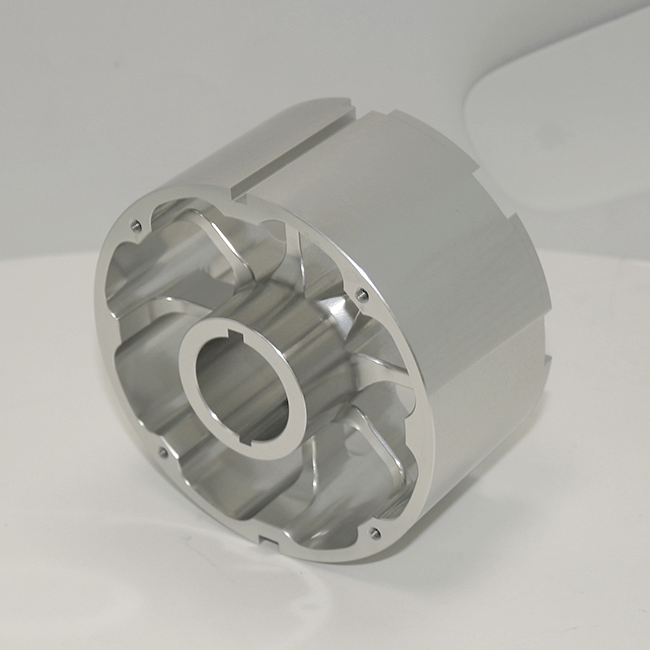
As manufacturing continues to evolve in the digital age, the adoption of high-speed machining techniques and cutting-edge tooling innovations is poised to reshape the industry landscape. By embracing innovation and investing in advanced machining solutions, manufacturers can stay ahead of the curve and unlock new levels of efficiency and performance in their operations.
In conclusion, the convergence of high-speed machining and cutting-edge tooling innovations represents a paradigm shift in the manufacturing industry, ushering in an era of unprecedented productivity and precision. With technology driving the way forward, the possibilities for innovation and advancement are limitless, propelling the industry towards new heights of success and prosperity.
Post time: Jun-14-2024