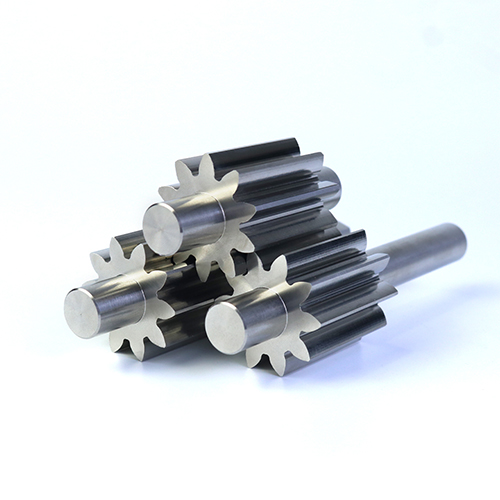
In the high-stakes world of energy production and industrial machinery, precision and efficiency are non-negotiable. The application of new technologies in turbine cylinder machining is transforming the manufacturing process, enabling breakthroughs in performance, durability, and sustainability. From power generation to aviation, advanced machining techniques are redefining how turbine cylinders are designed, produced, and maintained.
The Importance of Turbine Cylinder Machining
Turbine cylinders play a critical role in systems such as steam turbines, gas turbines, and hydroelectric generators. These components must endure extreme temperatures, pressures, and rotational speeds. Achieving the required precision during machining ensures:
●Optimal Efficiency: Minimizing energy loss during operation.
●Enhanced Durability: Prolonging the lifecycle of turbine components.
●Improved Safety: Reducing risks associated with high-stress environments.
Key Innovations in Turbine Cylinder Machining
1.High-Precision CNC Machining
Modern CNC (Computer Numerical Control) machines are setting new standards for accuracy in turbine cylinder production. These machines allow for:
●Micrometer-Level Precision: Meeting the stringent tolerances required for turbine efficiency.
●Complex Geometries: Enabling the production of intricate designs that optimize airflow and heat transfer.
●Reduced Waste: Minimizing material wastage through accurate cutting paths.
1.Additive Manufacturing Integration
Additive manufacturing, or 3D printing, is becoming a game-changer in turbine cylinder prototyping and repair:
●Rapid Prototyping: Accelerates the development of new turbine designs.
●Material Optimization: Allows for lightweight yet durable components.
●Localized Repairs: Enables precise restoration of worn or damaged areas, extending cylinder life.
1.Laser and Waterjet Cutting
Advanced cutting technologies like laser and waterjet systems are revolutionizing the initial shaping of turbine cylinders:
●Non-Contact Cutting: Reduces the risk of thermal damage.
●Versatility: Handles a wide range of materials, including superalloys commonly used in turbines.
●High-Speed Operations: Shortens production times while maintaining quality.
1.Robotic Automation
Robotic systems are enhancing consistency and efficiency in turbine cylinder machining:
●Automated Tool Changes: Reduces downtime between machining processes.
●Precision Handling: Ensures consistent quality across large production runs.
●AI-Powered Inspection: Identifies defects in real-time for immediate correction.
The Benefits of New Technologies in Turbine Machining
●Faster Production Cycles: Innovations like CNC automation and robotic systems significantly reduce machining time.
●Cost Efficiency: Optimized processes lower production costs without compromising quality.
●Sustainability: Reduced material waste and energy-efficient machines support environmental goals.
●Enhanced Performance: Precision machining results in turbine cylinders that boost operational efficiency and reliability.
Applications Across Industries
●Power Generation: Turbine cylinders are the heart of steam and gas turbines, critical for electricity production. New technologies ensure consistent performance, even in renewable energy setups like geothermal plants.
●Aerospace: Aircraft engines rely on turbine components to withstand extreme conditions. Advanced machining enables the production of lightweight, high-strength parts.
●Oil and Gas: Turbines used in offshore and onshore drilling benefit from robust cylinders machined to endure harsh environments.
What the Future Holds
The future of turbine cylinder machining lies in further integration of smart manufacturing, where AI and IoT-enabled machines will drive autonomous operations. Hybrid solutions combining subtractive and additive manufacturing will offer unparalleled flexibility, while sustainable practices will remain a priority.
Conclusion
The application of new technologies in turbine cylinder machining marks a pivotal moment for industries reliant on turbines. By adopting cutting-edge techniques, manufacturers are achieving unprecedented levels of precision, efficiency, and sustainability.
As the energy and industrial landscapes continue to evolve, turbine cylinder machining innovations will play a critical role in powering progress, from renewable energy to next-generation aircraft engines. Businesses that embrace these advancements will lead the way in shaping a future where precision meets performance.
Post time: Dec-16-2024