July 18, 2024 – As CNC machining technologies evolve in complexity and capability, the demand for skilled workers in the machining industry has never been more pressing. Discussions surrounding skill development and workforce training initiatives are essential to ensure that the industry can meet current and future challenges.
The Growing Complexity of CNC Machining
With advancements in CNC (Computer Numerical Control) machining, including the integration of automation and smart technologies, the skill set required for operators and programmers has expanded significantly. Modern CNC machines not only require knowledge of machining processes but also a strong understanding of software programming and system maintenance.
“Today's CNC operators must possess a blend of technical skills and analytical thinking,” says Mark Johnson, a senior CNC engineer. “The complexity of programming and operating these machines necessitates specialized training to maintain efficiency and quality.”
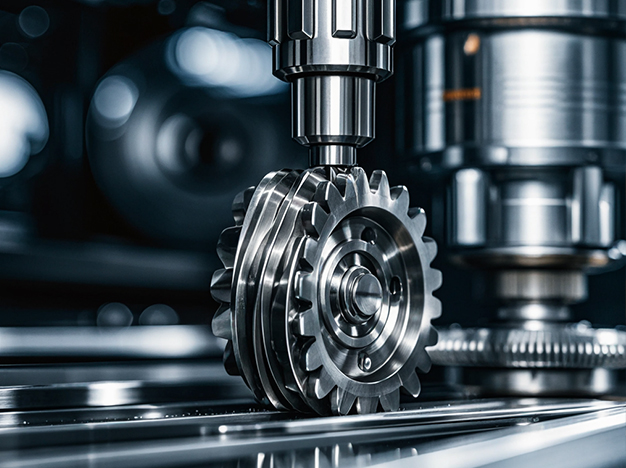
Specialized Training Programs
To address the skills gap, industry leaders and educational institutions are collaborating to develop specialized training programs. These programs focus on essential areas such as CNC programming, operation, and maintenance.
1.CNC Programming: Training initiatives are being designed to teach aspiring machinists the intricacies of G-code and M-code programming. This foundational knowledge is crucial for creating precise machining instructions.
2.Operational Training: Hands-on training in machine operation ensures that workers understand not only how to run a CNC machine but also how to troubleshoot common issues and optimize performance.
3.Maintenance Skills: With increased reliance on advanced machinery, maintenance training is vital. Programs emphasize preventive maintenance techniques to extend machine life and minimize downtime.
Attracting and Retaining Talent
As the machining industry faces a looming talent shortage, attracting and retaining skilled workers has become a priority. Employers are adopting various strategies to create a more appealing work environment.
1.Competitive Compensation: Many companies are reassessing their compensation packages to offer competitive wages and benefits that reflect the specialized skills required in the field.
2.Career Advancement Opportunities: Employers are promoting pathways for career growth, including mentorship programs and advanced training, to encourage long-term retention.
3.Engagement with Educational Institutions: Partnerships with technical schools and community colleges are essential for building a pipeline of skilled workers. Internships and co-op programs provide students with practical experience and exposure to the industry.
The Role of Technology in Training
Advancements in technology are also transforming workforce training. Virtual reality (VR) and augmented reality (AR) are increasingly being used to create immersive training experiences. These technologies allow trainees to practice CNC operation and programming in a safe and controlled environment.
“Using VR in training not only enhances understanding but also builds confidence in handling complex machinery,” notes Dr. Lisa Chang, a vocational education expert.
Looking Ahead
As the CNC machining landscape continues to change, ongoing investment in skill development and workforce training will be critical. Industry stakeholders must remain committed to fostering a skilled workforce capable of meeting the demands of a rapidly evolving market.
Conclusion
The future of CNC machining relies on the development of a skilled workforce equipped with the necessary tools and training. By investing in specialized training programs and creating an attractive environment for talent, the machining industry can ensure a robust pipeline of skilled professionals ready to tackle the complexities of modern machining technologies.
Post time: Aug-02-2024