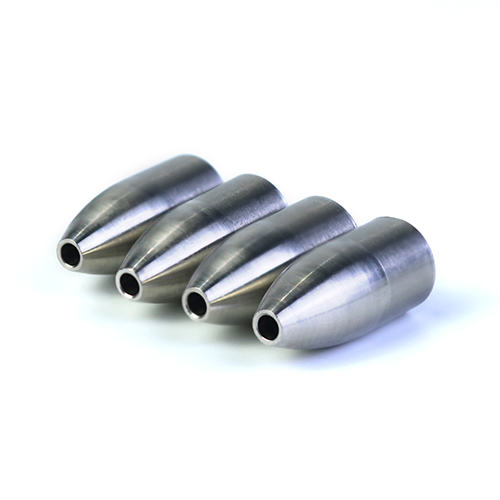
In the high-stakes world of manufacturing, where accuracy is critical and precision can make or break an industry, ultra-precision machining technology is leading the way. As industries demand ever-tighter tolerances, faster production, and superior quality, ultra-precision machining continues to revolutionize the manufacturing process. From aerospace to medical devices, electronics, and optics, this cutting-edge technology is transforming the way we build the future.
What is Ultra-Precision Machining?
Ultra-precision machining refers to the process of manufacturing components with micron and even nanometer-scale precision. Using techniques like precision grinding, diamond turning, laser ablation, and micro-milling, these methods produce parts with surface finishes and tolerances so fine they are practically flawless. Industries requiring impeccable detail—such as aerospace, automotive, medical, and semiconductors—are increasingly relying on ultra-precision machining to meet their high-performance needs.
The Evolution of Ultra-Precision Machining
Over the last few decades, ultra-precision machining technology has experienced remarkable advancements. While traditional precision machining focused on individual parts with tight tolerances, today’s automated, computer-controlled systems allow for faster, more complex productions with reduced human intervention. Automation, enhanced computational modeling, and cutting-edge equipment have increased both the speed and the consistency of these processes, making ultra-precision machining indispensable for modern manufacturing.
Key Technologies Shaping Ultra-Precision Machining
Several revolutionary technologies are powering today’s ultra-precision machining advancements:
● Precision Grinding and Polishing: These methods are used to achieve flawless surface finishes, which are essential for industries like optics, where even the smallest imperfections can affect functionality.
● Laser Ablation and Laser Machining: These techniques allow manufacturers to remove material with extreme accuracy at the micro and nano scale, particularly for semiconductor and microelectronics applications.
● Diamond Cutting and Tooling: Diamond tools, known for their hardness, are ideal for cutting hard materials like titanium and ceramics. This is especially important for aerospace and medical industries where durability and high tolerance are crucial.
● Nanotechnology: Nanotechnology is enabling the production of components with structures smaller than the wavelength of visible light, pushing the boundaries of precision and enabling breakthroughs in fields such as quantum computing and medical devices.
Industries Transformed by Ultra-Precision Machining
Ultra-precision machining is pivotal in industries where failure is not an option. Key sectors benefiting from these technologies include:
● Aerospace: Parts like turbine blades, engine components, and structural elements require ultra-tight tolerances to ensure safety and performance in high-stress, high-speed environments.
● Medical Devices: Implants, surgical instruments, and diagnostic devices need ultra-precision machining to meet stringent performance and biocompatibility standards.
● Semiconductors and Electronics: Ultra-precision machining is essential for creating microchips and semiconductor wafers that power everything from smartphones to space technology.
● Optics: Components like lenses, mirrors, and prisms must be manufactured with flawless surfaces and exact geometries, enabling high-performance optical systems used in telecommunications and scientific instruments.
Challenges in Ultra-Precision Machining
While ultra-precision machining has transformed manufacturing, there are still challenges that need to be addressed:
● Cost and Accessibility: The sophisticated equipment required for ultra-precision machining is expensive, making it a challenge for smaller manufacturers to access this technology. As demand increases, efforts are being made to make it more affordable and scalable.
● Material Limitations: Some materials—particularly advanced alloys or composite materials—can be difficult to machine at ultra-precise levels. Research and development into new tooling and cutting techniques are ongoing.
● Integration with Other Technologies: As the technology advances, integrating ultra-precision machining with other technologies like artificial intelligence, robotics, and real-time data analytics is crucial to optimize performance and reduce costs. This integration remains an ongoing challenge.
Looking Ahead: The Future of Ultra-Precision Machining
The future of ultra-precision machining holds incredible potential. With advancements in automation, machine learning, and nanotechnology, the level of precision achievable in manufacturing is expected to surpass current limits. Industries will continue to push for parts that are lighter, more durable, and more complex, which will drive further innovation in ultra-precision machining.
Additionally, as ultra-precision machining becomes more accessible, manufacturers of all sizes will be able to tap into its benefits. From reducing waste and material costs to improving product quality, the future is bright for ultra-precision machining.
Conclusion
The current status of ultra-precision machining technology is one of rapid innovation, with significant impacts across multiple industries. As manufacturers seek to push the boundaries of what is possible, ultra-precision machining will play an integral role in meeting the challenges of tomorrow. For those looking to stay competitive in an increasingly precise world, embracing ultra-precision machining technology is no longer a choice—it’s a necessity.
Post time: Dec-21-2024