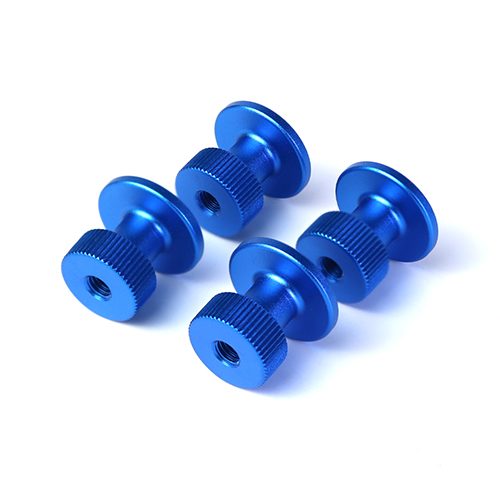
Unlocking Innovation: The Materials Behind Customized Part Manufacturing
In today’s fast-paced world, where precision and customization are the cornerstones of industrial success, understanding the materials used to process and customize parts has never been more important. From aerospace to automotive, electronics to medical devices, selecting the right materials for manufacturing impacts not only the functionality but also the durability and cost of the final product.
So, what materials are revolutionizing customized part production? Let’s take a closer look.
Metals: The Powerhouses of Precision
Metals dominate the manufacturing landscape due to their strength, durability, and versatility.
● Aluminum: Lightweight, corrosion-resistant, and easily machinable, aluminum is a favorite for aerospace, automotive, and electronics applications.
● Steel (Carbon and Stainless): Known for its toughness, steel is ideal for high-stress environments like machinery parts and construction tools.
● Titanium: Lightweight yet incredibly strong, titanium is a go-to material for aerospace and medical implants.
● Copper and Brass: Excellent for electrical conductivity, these metals are widely used in electronic components.
Polymers: Lightweight and Cost-Effective Solutions
Polymers are increasingly popular for industries requiring flexibility, insulation, and reduced weight.
- ABS (Acrylonitrile Butadiene Styrene): Strong and cost-effective, ABS is commonly used in automotive parts and consumer electronics.
- Nylon: Known for its wear resistance, nylon is favored for gears, bushings, and industrial components.
- Polycarbonate: Durable and transparent, it’s widely used in protective equipment and lighting covers.
- PTFE (Teflon): Its low friction and high heat resistance make it ideal for seals and bearings.
Composites: Strength Meets Lightweight Innovation
Composites combine two or more materials to create parts that are lightweight yet strong, a key requirement in modern industries.
● Carbon Fiber: With its high strength-to-weight ratio, carbon fiber is redefining possibilities in aerospace, automotive, and sports equipment.
● Fiberglass: Affordable and durable, fiberglass is commonly used in construction and marine applications.
● Kevlar: Known for its exceptional toughness, Kevlar is often used in protective gear and high-stress machinery parts.
Ceramics: For Extreme Conditions
Ceramic materials like silicon carbide and alumina are essential for applications requiring high-temperature resistance, such as in aerospace engines or medical implants. Their hardness also makes them ideal for cutting tools and wear-resistant parts.
Specialty Materials: The Frontier of Customization
Emerging technologies are introducing advanced materials designed for specific applications:
● Graphene: Ultra-light and highly conductive, it’s paving the way for next-gen electronics.
● Shape-Memory Alloys (SMA): These metals return to their original shape when heated, making them ideal for medical and aerospace applications.
● Bio-compatible Materials: Used for medical implants, they are designed to integrate seamlessly with human tissue.
Matching Materials to Manufacturing Processes
Different manufacturing techniques demand specific material properties:
● CNC Machining: Best suited for metals like aluminum and polymers like ABS due to their machinability.
● Injection Molding: Works well with thermoplastics like polypropylene and nylon for mass production.
● 3D Printing: Ideal for rapid prototyping using materials like PLA, nylon, and even metal powders.
Conclusion: Materials Driving Tomorrow’s Innovations
From cutting-edge metals to advanced composites, the materials used to process and customize parts are at the heart of technological advancement. As industries continue to push boundaries, the search for more sustainable, high-performance materials is intensifying.
Post time: Nov-29-2024