precis servic cnc
Our precision servo CNC services provide you with high-precision and high-efficiency CNC machining solutions to meet your manufacturing needs for complex precision parts.
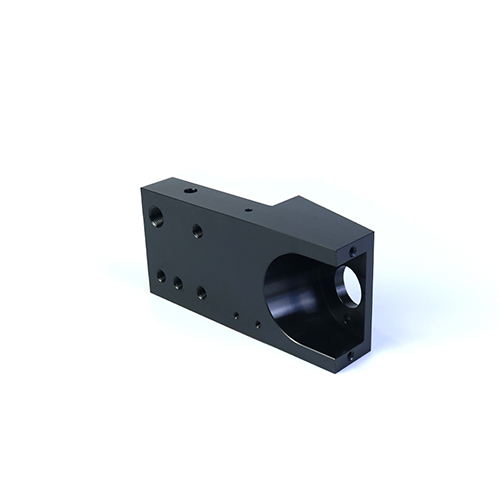
1、 Advanced equipment and technology
High performance CNC system
We adopt advanced CNC systems with high-speed processing capabilities and precise motion control functions. This system can achieve multi axis linkage control, ensuring the accuracy and stability of tool paths in complex machining processes. At the same time, the CNC system has a friendly human-machine interface, easy operation, and is easy to program and debug.
Precision servo motors and drivers
Equipped with high-precision servo motors and drivers, it can provide precise position, speed, and torque control. Servo motors have fast response speed and high precision, enabling precise control of small displacements, thereby ensuring the accuracy and surface quality of machined parts. The driver has good dynamic performance and stability, which can effectively suppress interference and ensure the smooth operation of the motor.
High precision machine tool structure
The machine tool is made of high-strength cast iron material, with optimized structural design and precision machining, and has good rigidity and stability. The guide rails and screws of the machine tool are equipped with high-precision linear guides and ball screws to ensure smooth and accurate motion. At the same time, the machine tool is equipped with advanced cooling and lubrication systems, effectively reducing thermal deformation and wear during the machining process, and extending the service life of the machine tool.
2、 Rich processing capability
Multiple material processing
We can process various metal materials such as aluminum alloy, stainless steel, titanium alloy, as well as engineering plastics, composite materials, etc. We have developed corresponding processing techniques based on the characteristics of different materials to ensure processing quality and efficiency.
Complex shape processing
With advanced CNC technology and rich processing experience, we can process various complex shaped parts, such as curved surfaces, irregular structures, thin-walled parts, etc. We can meet your needs for complex components in the aerospace industry, as well as precision parts in industries such as medical equipment and electronic devices.
High precision machining
Our precision servo CNC service can achieve micrometer level machining accuracy, ensuring that the dimensional accuracy, shape accuracy, and positional accuracy of parts meet strict requirements. By adopting advanced measuring equipment and detection methods, real-time monitoring and quality inspection of the machining process are carried out to timely detect and correct machining errors, ensuring the quality stability of the parts.
3、 Strict quality control
Raw material inspection
Before processing, we conduct strict inspections on the raw materials to ensure that their quality meets national standards and customer requirements. Test the chemical composition, mechanical properties, dimensional accuracy, etc. of raw materials to prevent the use of unqualified materials.
Process monitoring
During the machining process, we use advanced monitoring systems to monitor machining parameters in real-time, such as cutting speed, feed rate, cutting force, etc. By analyzing and adjusting these parameters, ensure the stability and consistency of the machining process. At the same time, our technicians will conduct regular spot checks on the processed parts to promptly identify and resolve any issues that arise during the machining process.
Finished product inspection
After processing, we conduct a comprehensive inspection of the finished parts, including testing of dimensional accuracy, shape accuracy, surface quality, hardness, and other aspects. We use high-precision coordinate measuring instruments, microscopes, hardness testers and other testing equipment to ensure that the quality of the parts meets the design requirements. Only parts that have passed strict inspection can be delivered to customers.
4、 Personalized customization service
Process optimization
Our technical team will provide you with personalized process optimization solutions based on your part design requirements and usage scenarios. By optimizing the processing technology, we can improve processing efficiency, reduce costs, and ensure the quality and performance of the parts.
Customized with special requirements
If you have special requirements for parts, such as special surface treatment, special tolerance requirements, etc., we will be dedicated to serving you. We will communicate fully with you, understand your needs, and develop corresponding solutions to meet your personalized needs.
5、 High quality after-sales service
technical support
We provide customers with comprehensive technical support, including processing technology consulting, programming guidance, equipment maintenance, and other services. No matter what problems you encounter during use, our technicians will provide timely assistance and solutions for you.
Equipment maintenance and upkeep
We regularly maintain and upkeep the equipment to ensure stable and reliable performance. At the same time, we also provide equipment maintenance training for customers to help them master the daily maintenance and upkeep methods of equipment, and extend the service life of equipment.
quick response
We have established a comprehensive after-sales service system that can quickly respond to customer needs. After receiving feedback from the customer, we will contact them immediately and arrange for technical personnel to go to the site to solve the problem, ensuring that the customer's production is not affected.
In short, our precision servo CNC services provide you with high-quality CNC machining solutions with advanced equipment, exquisite technology, strict quality control, personalized customization services, and high-quality after-sales service. Choosing us means choosing professionalism, quality, and peace of mind
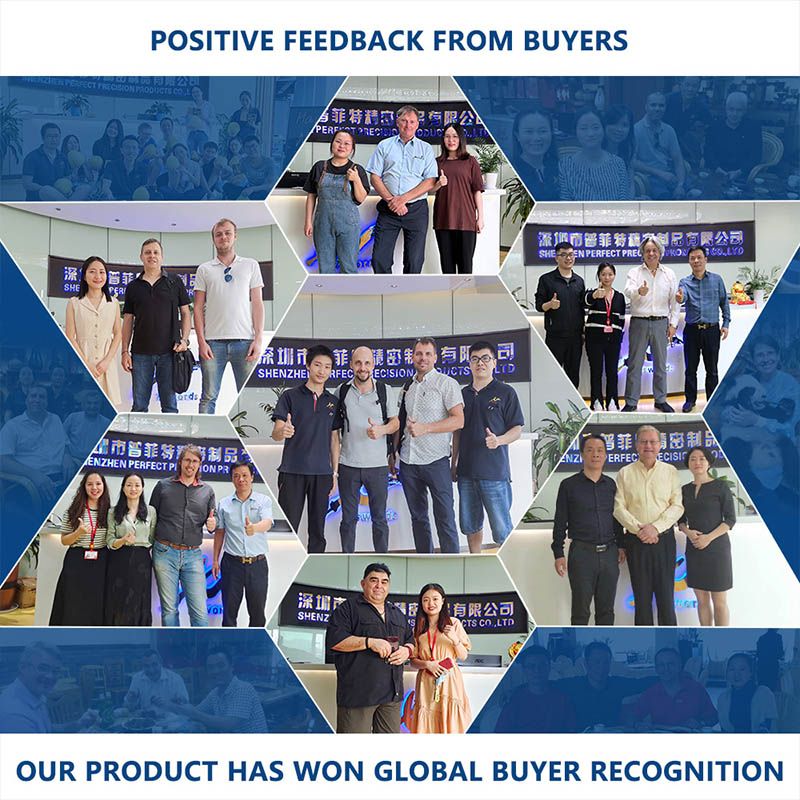
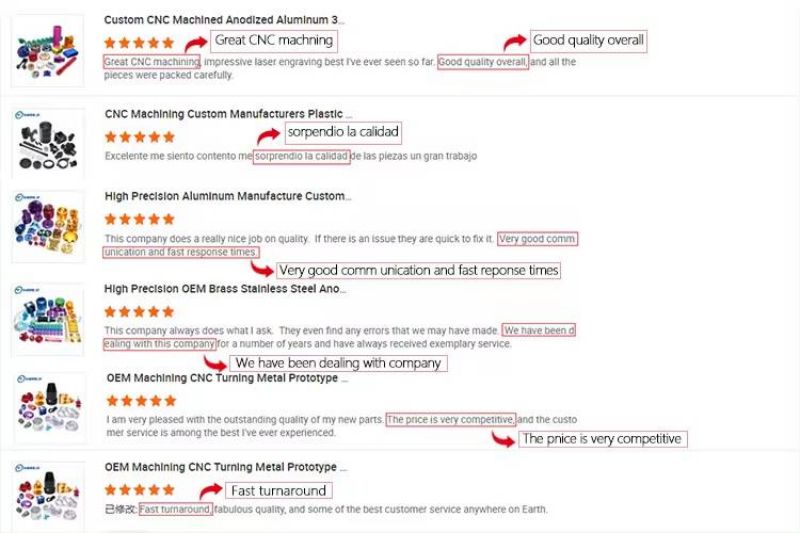
1、 Service Overview
Q1: What is precision servo CNC service?
A: Precision servo CNC service is the use of advanced CNC technology and precision servo systems to provide high-precision and complex shape machining services for various materials. We manufacture parts and products that meet strict precision requirements for our customers by precisely controlling the motion and processing parameters of the machine tool.
Q2: Which industries are your precision servo CNC services suitable for?
A: Our services are widely used in various industries such as aerospace, automotive manufacturing, medical equipment, electronic devices, and mold manufacturing. Whether it is the high-end manufacturing industry that requires high-precision components or other fields that have strict requirements for product quality and accuracy, we can provide high-quality CNC services.
2、 Equipment and Technology
Q3: What type of CNC equipment and technology are you using?
A: We adopt advanced numerical control systems, equipped with high-precision servo motors, drivers, and precise machine tool structures. These devices and technologies can achieve multi axis linkage machining, ensuring high-precision manufacturing of complex shaped parts. At the same time, we constantly update and upgrade our equipment to maintain a leading position in the industry.
Q4: How to ensure machining accuracy?
A: We ensure machining accuracy through the following aspects: Firstly, the equipment itself has high-precision mechanical components and advanced control systems, which can achieve micrometer level positioning accuracy and repeatability. Secondly, our technicians have extensive experience in programming and process planning, carefully optimizing to reduce machining errors. In addition, we also adopt strict quality inspection methods to monitor and measure the parts in real-time during the machining process, ensuring that the parts meet the design requirements.
Q5: What materials can be processed?
A: We can process various materials, including but not limited to aluminum alloy, stainless steel, titanium alloy, copper alloy, engineering plastics, etc. Different materials require different processing techniques and tool selection. We will develop the most suitable processing plan based on customer needs and material characteristics.
3、 Processing capability and process
Q6: What size of parts can you process?
A: We can process parts of various sizes, from small precision parts to large structural parts, all within our processing range. The specific size limit depends on the specifications of the machine tool and the customer's needs. After receiving the order, we will select the appropriate machine tool for processing based on the size and processing requirements of the parts.
Q7: What are the advantages of processing complex shaped parts?
A: Our precision servo CNC system can achieve multi axis linkage machining, which allows us to easily process various complex shaped parts, such as curved surfaces, irregular structures, thin-walled parts, etc. Through precise programming and tool path control, we can ensure the shape accuracy and surface quality of the parts, meeting customers' design requirements for complex parts.
Q8: What is the processing flow?
A: The processing flow usually includes the following steps: Firstly, the customer provides design drawings or samples of the parts, and our technicians analyze and evaluate the drawings to determine the processing technology and plan. Then, proceed with raw material procurement and preparation. Next, machining will be carried out on a CNC machine, and multiple quality inspections will be conducted during the machining process. After processing, the parts are subjected to surface treatment, cleaning, and packaging. Finally, deliver the finished product to the customer.
4、 Quality Control and Testing
Q9: How to carry out quality control?
A: We have established a comprehensive quality control system, with strict standards and processes for raw material inspection, processing monitoring, and finished product testing. In the raw material procurement process, we only select material suppliers that meet quality standards and inspect each batch of raw materials. During the machining process, we monitor the machining parameters in real-time through a numerical control system, and technicians also conduct regular spot checks on the parts. After processing, we use high-precision measuring equipment such as coordinate measuring instruments, microscopes, etc. to comprehensively inspect the size, shape, surface roughness, etc. of the parts to ensure that the quality of the parts meets customer requirements.
Q10: How to deal with quality issues?
A: If quality problems are found during the processing, we will immediately stop the processing, analyze the cause of the problem, and take corresponding corrective measures. If there is a quality issue with the finished parts, we will negotiate a solution with the customer based on the specific situation, which may include reprocessing, repairing, or replacing the parts. We always aim for customer satisfaction and ensure that the quality of the parts delivered to customers is qualified.
5、 Price and Delivery
Q11: How is the price determined?
A: The price mainly depends on factors such as the material, size, complexity, processing accuracy requirements, and order quantity of the parts. We will conduct detailed cost accounting and provide a reasonable quotation after receiving the customer's design drawings or requirements. At the same time, we will also provide optimized processing solutions based on customers' budgets and needs to achieve the best cost-effectiveness.
Q12: What is the delivery cycle?
A: The delivery cycle may vary depending on the complexity, quantity, and current production schedule of the parts. Generally speaking, simple parts may be delivered within 1-2 weeks, while complex parts may take 3-4 weeks or longer. After receiving the order, we will communicate with the customer to determine the delivery date and make every effort to deliver on time. If customers have urgent needs, we will also do our best to coordinate resources and accelerate production progress.
6、 After sales service
Q13: What after-sales services are provided?
A: We provide comprehensive after-sales service, including technical support, equipment maintenance, parts repair, etc. If customers encounter problems during the use of parts, our technicians will provide timely solutions. In addition, we also provide equipment maintenance training for customers to help them better maintain and use CNC equipment.
Q14: What is the response time for after-sales service?
A: We attach great importance to the response speed of after-sales service. Generally, we will respond within 24 hours after receiving customer feedback and arrange technical personnel to go to the site to solve the problem according to the urgency of the issue. We are committed to providing timely and efficient after-sales service to our customers, ensuring that their production is not affected.
I hope the above content can meet your needs. If you have any other questions, please feel free to contact us at any time.