Titanium Alloy Aerospace Precision Machining Parts
Product Overview
In the highly demanding field of aerospace engineering, the need for precision, durability, and reliability cannot be overstated. Whether it’s for aircraft components, spacecraft, or defense systems, aerospace manufacturers require materials and parts that perform under extreme conditions. Among the most sought-after materials for this purpose is titanium alloy, known for its exceptional strength-to-weight ratio, corrosion resistance, and high-temperature performance. When these alloys are precision-machined to exacting standards, they result in Titanium Alloy Aerospace Precision Machining Parts that are critical to the success of modern aerospace applications.
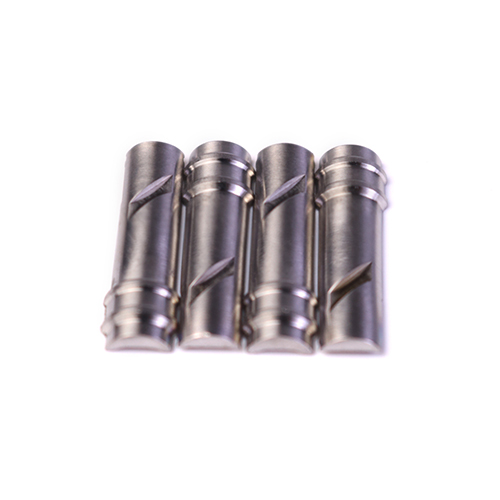
What Are Titanium Alloy Aerospace Precision Machining Parts?
Titanium alloys are a group of metal alloys primarily made from titanium, known for their superior mechanical properties, including outstanding strength, lightweight characteristics, and resistance to high temperatures and corrosion. Titanium alloy aerospace precision machining parts are components created from these alloys using advanced CNC machining processes. The machining process involves the precise cutting, shaping, and finishing of titanium alloy parts to meet exact specifications, ensuring that the components perform reliably even in the most challenging environments.
Precision machining involves highly accurate equipment and tools that can achieve the tight tolerances required for aerospace parts. When titanium alloys are machined, the result is a range of parts used in the construction of critical aerospace structures and systems, such as engine components, airframes, fasteners, and landing gear.
Key Benefits of Titanium Alloy Aerospace Precision Machining Parts
1. Exceptional Strength-to-Weight Ratio
One of the primary reasons titanium alloys are preferred in aerospace is their incredible strength-to-weight ratio. These alloys deliver the strength needed to withstand the harsh conditions of flight while being lighter than many other materials. This property is especially beneficial in aerospace, where reducing weight without compromising strength improves fuel efficiency and overall performance.
2. Superior Corrosion Resistance
Titanium alloys are highly resistant to corrosion, making them ideal for use in environments exposed to moisture, seawater, or extreme temperatures. In aerospace, parts made from titanium alloys are less prone to wear and degradation, which ensures longevity and reduces the risk of part failure in critical systems.
3. High-Temperature Resistance
Aerospace applications often involve components exposed to extremely high temperatures, such as engine parts. Titanium alloys maintain their strength and structural integrity even at elevated temperatures, ensuring that parts perform reliably under the heat generated during flight.
4. Durability and Longevity
Titanium alloys are not only corrosion-resistant but also incredibly durable. Parts made from these materials are designed to endure harsh operational conditions for extended periods, reducing the need for frequent maintenance or replacements in aerospace systems.
5. Precise Engineering for Complex Geometries
Precision machining allows manufacturers to produce complex geometries and intricate designs with a high degree of accuracy. This is especially important in the aerospace industry, where components must fit perfectly within larger systems. Whether creating lightweight structural elements or intricate engine parts, precision machining ensures a perfect fit and optimal performance.
1. Aircraft Engines
Titanium alloy parts are widely used in aircraft engines due to their ability to withstand high temperatures, pressures, and stresses. Components such as turbine blades, compressor discs, and casings are often made from titanium alloys to ensure performance and safety.
2. Airframe Components
The airframe of an aircraft, which includes the wings, fuselage, and tail section, often features titanium alloy parts. These parts provide the necessary strength and rigidity while keeping the weight to a minimum, contributing to the overall efficiency and maneuverability of the aircraft.
3. Landing Gear and Structural Components
Landing gear and other critical structural components, such as frames and supports, must be robust and durable. Titanium alloys offer the strength needed to withstand the forces experienced during takeoff, landing, and while on the ground, ensuring safe operations for both commercial and military aircraft.
4. Spacecraft and Satellites
Titanium alloys are essential in space exploration and satellite manufacturing, where components must endure extreme conditions, including intense heat and the vacuum of space. Precision-machined titanium parts are used in various spacecraft systems, including propulsion systems, structural elements, and communication devices.
5. Military and Defense
Military and defense applications require parts that are not only strong and lightweight but also resistant to corrosion in harsh environments. Titanium alloys are used in the production of military aircraft, helicopters, naval vessels, and defense systems to ensure reliability in critical missions.
The performance of aerospace systems directly impacts safety, efficiency, and operational costs. High-quality titanium alloy aerospace precision machining parts provide the strength, reliability, and durability required for the most demanding applications. By choosing titanium alloy parts that are precisely machined, aerospace manufacturers ensure that they are investing in components that will support long-term performance and meet rigorous safety standards.
Titanium alloy aerospace precision machining parts are an integral part of modern aerospace engineering, providing unmatched strength, durability, and performance. From aircraft engines to spacecraft components, titanium alloys help ensure that aerospace systems operate safely and efficiently in some of the most demanding environments. By choosing precision-machined titanium alloy parts, manufacturers can ensure that their components meet the highest standards of performance, reliability, and safety.
For businesses looking to remain competitive in the aerospace sector, investing in high-quality titanium alloy aerospace precision machining parts is a step toward engineering excellence and future success.
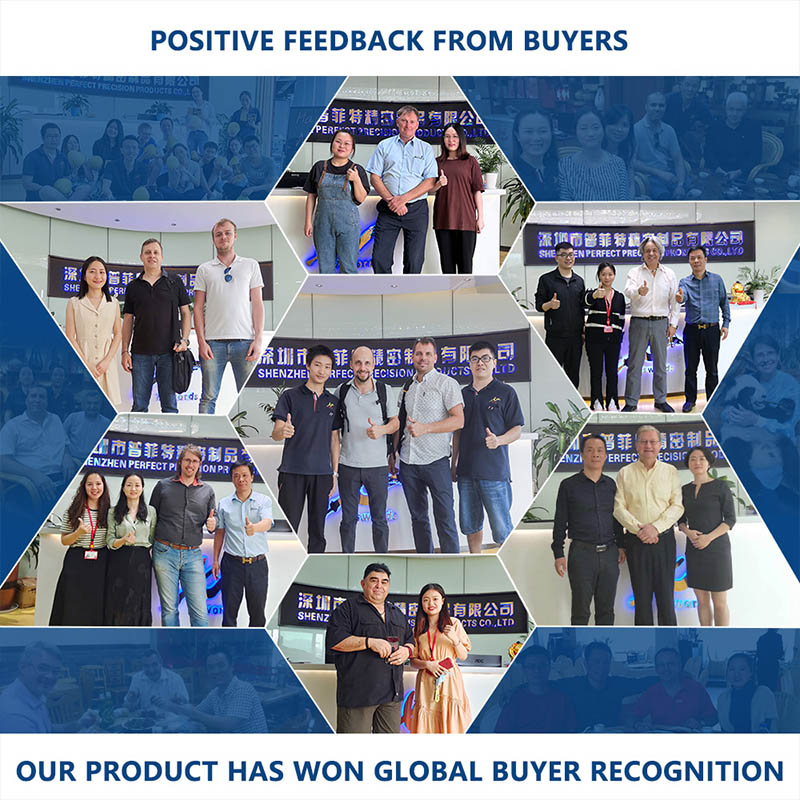
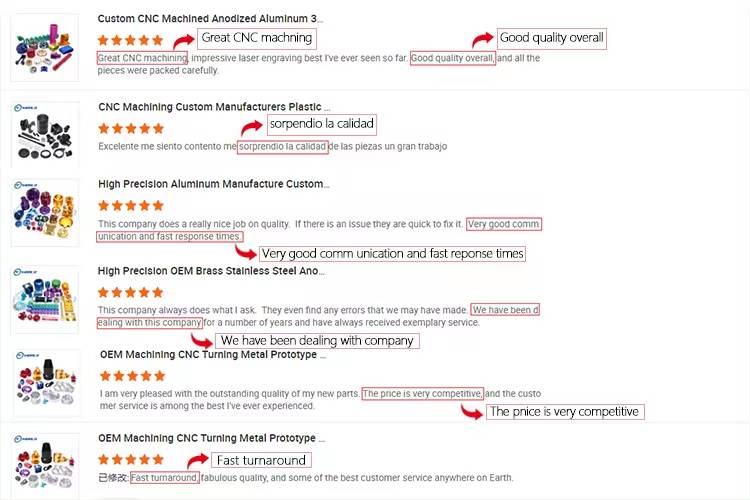
Q:How Precise Are Titanium Alloy Aerospace Machining Parts?
A:Titanium alloy aerospace precision machining parts are manufactured with high accuracy, often to tolerances as tight as 0.0001 inches (0.0025 mm). The precision machining process ensures that even the most complex geometries and designs are fabricated to meet the exact requirements of aerospace applications. This high level of accuracy is crucial for ensuring the integrity and performance of critical aerospace systems.
Q:How Are Titanium Alloy Aerospace Parts Tested for Quality?
A:Titanium alloy aerospace parts undergo rigorous quality control and testing, including:
·Dimensional Inspection: Using coordinate measuring machines (CMM) and other advanced tools to ensure parts meet tight tolerances.
· Material Testing: Verifying the chemical composition and mechanical properties of titanium alloys to ensure they meet aerospace standards.
·Non-Destructive Testing (NDT): Methods such as X-ray, ultrasonic, and dye penetrant testing are used to detect any internal or surface defects without damaging the parts.
· Fatigue Testing: Ensuring that parts can withstand cyclic loads and stresses over time without failure.
Q:What Are the Most Common Types of Titanium Alloys Used in Aerospace?
A:The most commonly used titanium alloys for aerospace applications include:
·Grade 5 (Ti-6Al-4V): The most widely used titanium alloy, offering a great balance of strength, corrosion resistance, and lightweight properties.
·Grade 23 (Ti-6Al-4V ELI): A higher-purity version of Grade 5, providing better fracture toughness and used in critical aerospace components.
·Grade 9 (Ti-3Al-2.5V): Offers excellent strength and is often used in airframes and aircraft structures.
·Beta Alloys: Known for their high strength, beta titanium alloys are used in components that require exceptional load-bearing capabilities.
Q:What Is the Typical Lead Time for Titanium Alloy Aerospace Parts?
A:Lead time for titanium alloy aerospace precision machining parts can vary based on the complexity of the part, order quantity, and the manufacturer’s capabilities. Generally, lead times can range from two to six weeks, depending on these factors. For urgent projects, many manufacturers offer expedited services to meet tight deadlines.
Q: Are Small Batches of Titanium Alloy Aerospace Parts Possible?
A:Yes, many manufacturers can produce small batches of titanium alloy aerospace parts. CNC machining is highly versatile and suitable for both low-volume and high-volume production runs. Whether you need a handful of parts for prototyping or a larger order for production, precision machining can be tailored to meet your needs.
Q:What Makes Titanium Alloy Aerospace Parts Cost-Effective?
A:Although titanium alloys can be more expensive than other materials upfront, their durability, corrosion resistance, and performance in extreme conditions make them cost-effective in the long term. Their long lifespan, reduced need for maintenance, and ability to perform without failure in critical aerospace applications can lead to significant cost savings over time.