Turbine Manufacturing
Product Overview
Turbines are integral to a wide array of industries, from energy production to aerospace and beyond. These powerful machines are responsible for converting fluid energy—whether it’s steam, gas, or water—into mechanical energy, driving various systems and processes with unparalleled efficiency. The rise of factory manufacturing has revolutionized turbine production, ensuring that these critical components are not only produced to the highest standards of precision but also cater to the increasingly complex needs of modern industries. Let’s take a deeper dive into the world of turbine manufacturing and its impact on global industries.
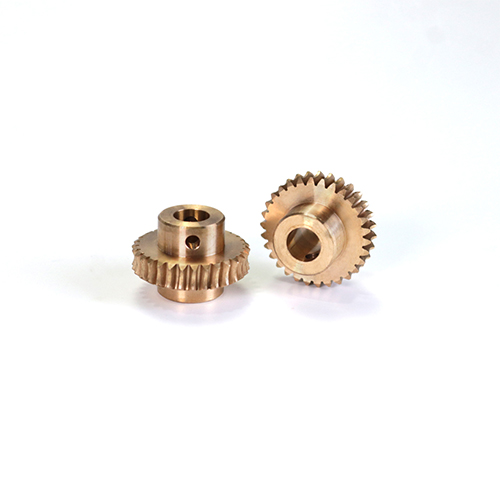
At its core, a turbine is a machine that harnesses the energy from moving fluids (liquids or gases) to perform mechanical work. The most common types of turbines include:
●Steam Turbines: Often used in power plants to convert steam into electricity.
●Gas Turbines: Common in power generation, aviation, and industrial settings, they convert gas flow into energy.
●Hydraulic (Water) Turbines: Used in hydropower plants to convert the energy of flowing water into electrical power.
Turbines play a critical role in the production of energy, powering everything from electric grids to aircraft, while also being pivotal in industrial manufacturing processes.
Factory manufacturing has played a transformative role in turbine production, enabling large-scale, efficient, and precise manufacturing processes that are essential for creating high-performance turbines. Turbine manufacturing involves highly specialized processes that combine advanced materials, precise engineering, and cutting-edge technology to meet stringent performance and reliability standards.
1.Precision Engineering
The manufacturing of turbines requires exceptional precision. With the advancement of Computer Numerical Control (CNC) machining, additive manufacturing (3D printing), and other precision techniques, factories can produce turbines with extremely tight tolerances. This ensures that the turbines perform efficiently and reliably in demanding environments. Whether it’s the intricate blades of a gas turbine or the large, robust structure of a steam turbine, precision manufacturing is crucial for the turbine’s performance and longevity.
2.Customization and Flexibility
One of the primary advantages of factory manufacturing is the ability to customize turbines for specific applications. Industries across the board—whether in energy production, aerospace, or marine—often require turbines with unique specifications. Factories can tailor the turbine's size, material, and design to meet the exact needs of the client, ensuring optimized performance for each use case.
3.High-Quality Materials
The materials used in turbine manufacturing must withstand extreme temperatures, pressures, and mechanical stresses. Factory manufacturing employs advanced materials such as high-performance alloys, ceramics, and composites to create turbines capable of enduring these tough conditions. This results in turbines that are not only powerful but also durable, ensuring a long operational life and minimal maintenance needs.
4.Cost Efficiency through Mass Production
The scale of factory manufacturing also offers cost efficiency. With large-scale production capabilities, manufacturers can reduce costs by optimizing processes, utilizing automation, and maintaining strict quality control standards. These efficiencies are passed on to the customer, resulting in high-quality turbines at a more competitive price.
5.Quality Control and Testing
Quality control is a cornerstone of factory turbine manufacturing. Each turbine is subjected to rigorous testing to ensure it meets performance, safety, and durability standards. From load testing to vibration analysis, turbines undergo multiple stages of quality assurance before being shipped to the customer. This attention to detail guarantees that the final product will perform under even the most demanding conditions.
1.Energy Production
Turbines are a backbone of power generation, whether it’s fossil fuels, nuclear energy, or renewable sources like wind and hydropower. Factory-manufactured turbines are used in power plants worldwide to generate electricity. Gas turbines and steam turbines are commonly used in both traditional and renewable energy plants, playing a crucial role in meeting the world’s growing energy needs.
2.Aerospace
In the aerospace industry, gas turbines (jet engines) are essential for powering aircraft. The manufacturing of aerospace turbines demands the highest standards of precision, as these turbines need to operate efficiently at high speeds and altitudes. Factory-produced turbines provide the performance and reliability necessary for both commercial and military aviation.
3.Marine and Naval
Turbines also play a critical role in the marine industry. Marine turbines are used in ships, submarines, and other vessels, converting the energy from fuel or steam into mechanical power to propel ships across the water. As the maritime industry embraces more eco-friendly technologies, the demand for highly efficient and reliable turbines continues to rise.
4.Industrial Manufacturing
Many industries rely on turbines to drive large-scale machinery in production lines, compressors, pumps, and other mechanical systems. Factory-made turbines ensure that these processes run efficiently, minimizing downtime and maximizing production output.
5.Renewable Energy
Wind turbines have become a significant part of the renewable energy landscape, generating electricity from wind power. Factories specializing in renewable energy turbine manufacturing have played a pivotal role in advancing the efficiency, reliability, and scalability of wind turbines to meet global energy needs.
As the world shifts towards more sustainable and energy-efficient solutions, the turbine manufacturing industry is undergoing significant innovation. Several key trends are shaping the future of turbine manufacturing:
Advancements in Materials: The continued development of lighter, stronger materials will enable turbines to operate at even higher efficiencies and withstand extreme conditions.
Hybrid and Renewable Turbines: There is growing interest in combining turbine technology with renewable energy sources like wind, solar, and hydrogen to reduce carbon emissions and create more sustainable energy systems.
Smart Turbines: The integration of sensors and real-time data monitoring systems will allow turbines to operate more efficiently by providing operators with predictive maintenance insights and real-time performance data.
Additive Manufacturing: 3D printing and other additive manufacturing technologies are being explored to create more complex and customized turbine parts with less material waste and faster production times.
Turbine manufacturing is at the forefront of industrial innovation, providing the power that drives economies, industries, and even nations. Factory-made turbines are essential to ensuring the optimal performance of critical systems in energy production, aerospace, marine, and industrial manufacturing. With the continuous evolution of precision engineering, materials science, and manufacturing technologies, turbines will remain key players in the development of more efficient, sustainable, and reliable systems for generations to come.
Whether you’re looking for cutting-edge solutions in renewable energy, aerospace innovation, or industrial machinery, factory-made turbines are the driving force behind modern progress, powering industries forward into a more efficient and sustainable future.
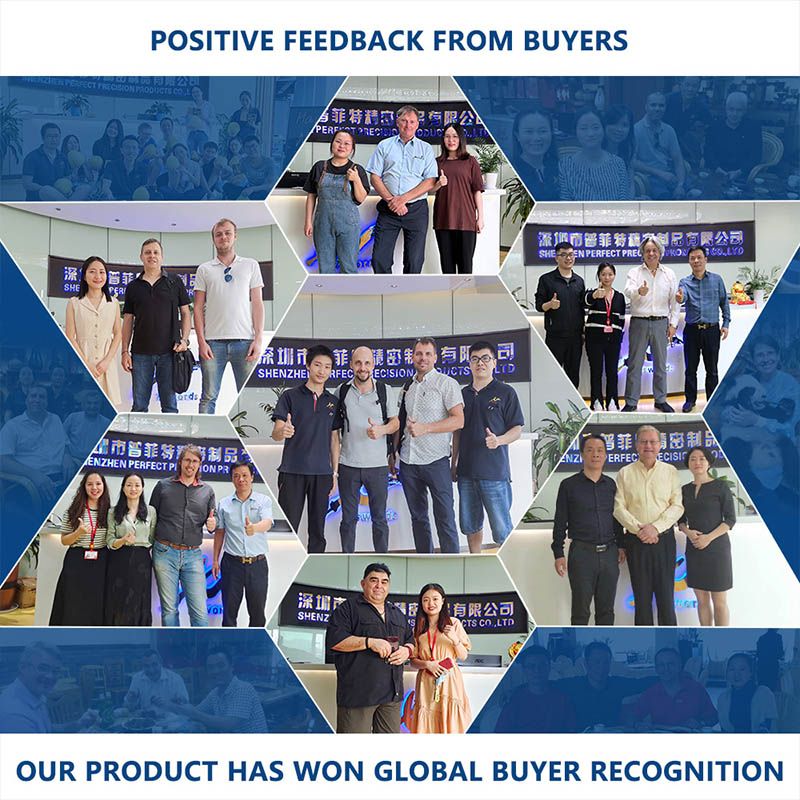
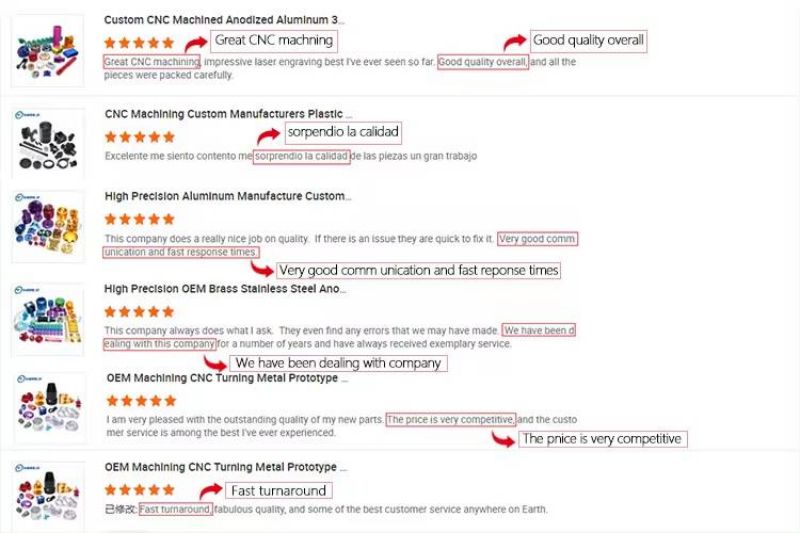
Q:What materials are used in turbine manufacturing?
A:Turbine components are made from high-performance materials capable of withstanding extreme temperatures, pressures, and mechanical stresses. Common materials include:
●Alloys (e.g., nickel, titanium, stainless steel) for strength and heat resistance
●Ceramics for high-temperature applications
●Composites for lightweight yet strong structures
●Advanced coatings to reduce wear and corrosion
Q:How are turbines manufactured?
A:Turbine manufacturing involves several steps, including:
●Design and engineering: Turbines are designed using advanced CAD software, with precise specifications tailored to the intended application.
●Precision machining: Components like blades, rotors, and shafts are manufactured with high accuracy using CNC (Computer Numerical Control) machining and other precision techniques.
●Assembly: Parts are carefully assembled, ensuring tight tolerances and optimal performance.
●Testing and quality control: Turbines undergo rigorous testing, including load tests, vibration analysis, and material stress testing to ensure reliability and efficiency.
Q:How do manufacturers ensure the quality of turbines?
A:Quality assurance in turbine manufacturing includes:
●Precision testing: Turbines undergo various tests, including flow simulations, vibration tests, material stress tests, and load testing to verify performance.
●Material inspections: The quality of materials used is inspected to ensure they meet the necessary strength, durability, and corrosion resistance standards.
●Certification and compliance: Turbine manufacturers adhere to industry standards and certifications (e.g., ISO, ASME) to ensure turbines meet safety and regulatory requirements.
Q:Can turbines be customized for specific applications?
A:Yes, one of the key advantages of turbine manufacturing is customization. Turbines can be tailored to meet specific requirements, such as:
●Size and output capacity: Designed for different levels of power generation or propulsion.
●Materials: Specific materials chosen for unique environmental conditions (e.g., high temperatures, corrosive environments).
●Efficiency and performance: Modifications to improve efficiency, reduce emissions, or meet specific operational needs.
Q:How long do turbines typically last?
A:The lifespan of a turbine depends on factors such as the type of turbine, the materials used, and the conditions in which it operates. On average:
●Gas turbines: 20-25 years, depending on maintenance and operational conditions.
●Steam turbines: Can last 30-40 years with proper care and maintenance.
●Wind turbines: Typically last 20-25 years, though some parts, like blades, may require replacement during that period.
Proper maintenance, regular inspections, and timely repairs can extend the lifespan of a turbine and maintain its efficiency.
Q:How are turbines used in renewable energy?
A:Turbines play a key role in renewable energy generation, particularly in wind and hydropower. In wind energy, wind turbines harness the power of the wind to generate electricity. Similarly, in hydropower, turbines convert the energy of flowing water into electrical power. These renewable energy turbines contribute to reducing reliance on fossil fuels and help combat climate change.